Los residuos de espumas de poliuretano, como las que llevan las neveras y los automóviles, se podrían reutilizar potencialmente en matrices de yeso, según las pruebas que han realizado investigadores de la Universidad de Burgos.
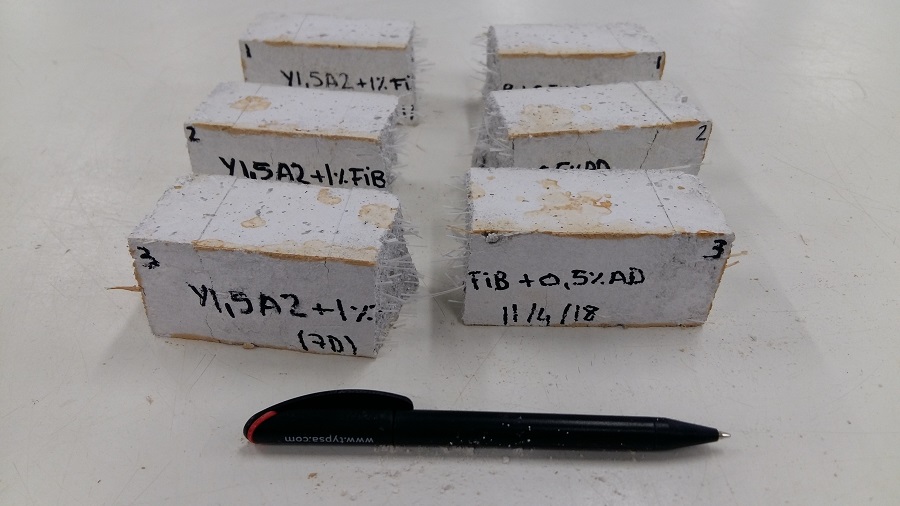
Los residuos de poliuretano constituyen un importante problema medioambiental. El uso de este plástico, presente en una amplia gama de productos comerciales –desde neveras y congeladores, en los que se utiliza como aislante, hasta colchones, componentes de automóviles o suelas de calzado– continúa creciendo. En la Unión Europea, se produjeron en 2017 más de 700.000 toneladas de poliuretano, de las cuales se estima que en torno a un 27% termina en vertederos.
Esta opción del vertido es la más común y a su vez la más desaconsejable cuando se obtienen residuos de este material. Otras, como la incineración para la producción de energía o el reciclaje, dando un segundo uso al plástico, son menos frecuentes. Pero, este último sobre todo, debe ser el camino a elegir.
El proyecto europeo LIFE-REPOLYUSE aborda la gestión del poliuretano mediante el uso de técnicas novedosas para su reutilización
Así lo contemplan los socios del proyecto europeo LIFE-REPOLYUSE, coordinado por la Universidad de Burgos (UBU), el cual aborda la problemática de la gestión del poliuretano mediante el uso de técnicas novedosas para su reducción y reutilización. En concreto, los investigadores están tratando de incorporar este residuo tratado a nuevos materiales de construcción, con el fin de prolongar su vida útil.
Y ya están obteniendo resultados: en un estudio publicado en la revista Polymers, han analizado el comportamiento de varias espumas de poliuretano procedentes de diversos tipos de industrias (refrigeración, automóvil y vehículos fuera de uso) y han evaluado su uso potencial en matrices de yeso.
Según indican Sara Gutiérrez González y Lourdes Alameda Cuenca Romero, del Grupo de Investigación en Ingeniería de Edificación (GIIE) de la UBU, los residuos de poliuretano se han caracterizado física, química y microscópicamente. Posteriormente, analizaron la posibilidad de incorporar estos residuos en una matriz de yeso y ensayaron mezclas, determinando su resistencia mecánica a la flexión y compresión, su reacción al fuego, su peso por unidad de área y su comportamiento térmico.
“Los resultados muestran que, en todos los casos, el residuo es inerte y no se produce lixiviación”, señalan las investigadoras. Asimismo, “el proceso de generación de los residuos determina la microestructura de la espuma, además de sus propiedades fisicoquímicas que afectan directamente a los materiales en los que están incluidos, lo que ofrece diferentes formas en que se pueden aplicar”, destacan.
Propiedades del nuevo material
Al incluir los residuos en matrices de yeso, obtuvieron una resistencia mecánica adecuada, una reducción de la conductividad térmica en un 33 % y una reducción en el peso del material en un 31%. En los ensayos de reacción al fuego, “solo dos tipos de residuos de espuma rígida de poliuretano cumplieron con los estándares para tener una clasificación A1, que es ideal para los materiales de revestimiento interior para edificios”, apuntan.
Otros dos tipos de espuma analizados mostraron peor comportamiento de reacción al fuego debido a las impurezas que contenían, sin embargo, “aún está por determinar si la clasificación en estos dos casos sería la de A2 o peor y habría que buscar formas alternativas de aplicar el material en diferentes áreas de un edificio”, subrayan.
El proyecto LIFE-REPOLYUSE, iniciado a finales de 2017 y que concluirá en septiembre de 2020, con un presupuesto cercano a los 400.000 euros, ha seguido avanzando. El consorcio, en el que participan las empresas Exergy Ltd, TECSA y Yesyforma Europa, ha completado ya la construcción del prototipo para fabricar las placas de yeso-poliuretano. A lo largo de este mes, avanzan, está prevista la colocación de las placas en el primer sitio demostrativo, en Miñano (Álava).
El equipo prevé lograr una reducción del 30% en el consumo de energía y del 17% en el consumo de agua del proceso de construcción, además de una rebaja del 18% en los costes de fabricación, en comparación con los productos existentes en el mercado.
Fuente:
Sinc