Un equipo conjunto de Airbus y FIDAMC ha fabricado una prueba de pieza de vuelo con materiales compuestos reciclados, utilizando para ello un nuevo método de fabricación aditiva que promete importantes ahorros en cuanto a costes y peso.
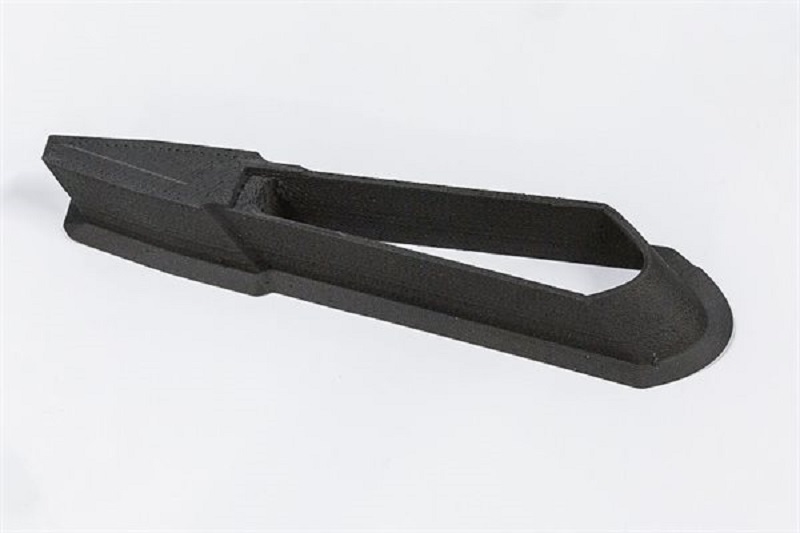
Cuña de borde de salida del elevador exterior de un A380 fabricado con material compuesto reciclado (prueba)
Si bien es cierto que sacar partido a los residuos no es ninguna novedad, sí lo es hacerlo a partir de restos de material compuesto para producir nuevas piezas. Esto es lo que ha conseguido el equipo de materiales y procesos de R&T, junto con ProtoSpace Getafe y FIDAMC. Juntos desarrollan un nuevo proceso de fabricación aditiva 3D real sin útiles de montaje que prevé importantes beneficios a lo largo de todo el ciclo de vida del producto, así como ahorros en cuestiones de peso y costes.
«Obtenemos filamentos para la fabricación aditiva de material compuesto a partir de desechos de CFRP (polímero reforzado con fibra de carbono) procedente de, por un lado, piezas ya fabricadas para obtener las fibras de refuerzo y, por otro, de la poliamida de materiales auxiliares, como las bolsas de vacío”, apunta Guillermo Hernáiz López, ingeniero de R&T.
Asimismo, un demostrador industrial con capacidad de impresión multimaterial en desarrollo por MTorres (empresa puntera en fabricación de máquina-herramienta para el material compuesto), previsto para finales de año, se encargará de procesar los diferentes materiales compuestos con el fin de alcanzar un elevado rito de producción. Así, el equipo ha conseguido su primer hito con la producción de una prueba de pieza de vuelo mediante fabricación aditiva con varios filamentos de material compuesto 100% reciclado.
El proyecto, que ha sido financiado por el Centro para el Desarrollo Tecnológico Industrial (CDTI), cuenta con los medios de impresión adecuados, así como con la definición de varias aplicaciones tecnológicas para las piezas de vuelo (carenados complejos, conductos y elementos estructurales, repuestos, etc.) y los medios de producción. Para la identificación de dichas aplicaciones, el equipo se coordina con el equipo multifuncional de Fabricación Aditiva de Illescas, lo que garantiza que las plantas se incorporen como clientes finales.
Además, con este nuevo método se ayudará a reducir la práctica actual de incinerar y enterrar los residuos de CFRP al final de su vida útil y a reutilizar el material auxiliar introduciendo ambos de nuevo en la línea de producción, lo que se traduce en un importante paso hacia las normas más restrictivas que están por venir.
Proporcionar una segunda vida a los materiales compuestos y materiales auxiliares no solo es una actividad más ecológica, sino que ademas incrementará los beneficios asociados al uso de piezas de material compuesto estándar. Y es que en la aeronáutica, donde la búsqueda de métodos más rentables y ecoeficientes no cesa, conceptos como el de “usar y tirar” se ven cada día más cuestionados.
Fuente:
FIDAMC