Las medidas adoptadas en la acería gipuzkoana están encaminadas a reducir los residuos, separar los aceites y disminuir el consumo de agua.
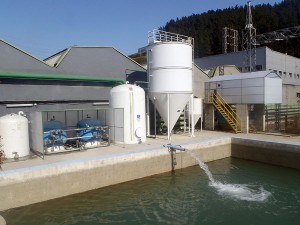
La planta de producción de acero de Gerdau en Azkoitia (Gipuzkoa) ha logrado importantes mejoras ambientales gracias a la aplicación de nuevas tecnologías y nuevos métodos de trabajo. Este compromiso de la empresa por asegurar un desarrollo sostenible, se ha centrado en tres campos: mejora de la eficiencia energética, optimización del uso del agua y reducción de la generación de residuos.
En el campo de la racionalización de los usos del agua, se han realizado diferentes acciones que han permitido un mayor índice de recirculación interna, reduciendo en el año 2013 un 50% su consumo, lo que equivale a captar del río 100.000 m3 de agua menos al año.
Entre dichas acciones destaca la inversión de más de 400.000 euros en una nueva depuradora para conseguir los estándares de calidad del agua necesarios que permitan su posterior reutilización interna y el cierre del circuito de agua del tren de laminación.
Por otro lado, se han sustituido los aires acondicionados de agua por otros de gas y se han cambiado cinco intercambiadores de calor que funcionaban con agua por intercambiadores que refrigeran con aire, modificaciones que han supuesto una inversión de 150.000€.
Por último, se han colocado contadores en toda la red de agua industrial, lo que posibilita un control de los consumos, detectando así las desviaciones inmediatamente.
Reducción de residuos
Durante el año 2013, se realizaron mejoras en el tratamiento de residuos de lodos de depuradora, con lo que se consiguió reducir la generación de residuos de 27,9 kg/t a 25,9 kg/t. Para lograr este resultado se ha modificado el circuito de aguas de refrigeración de la laminación y se ha construido un sistema de extracción de fangos, que los envía a un filtro prensa en el que se procede a su deshidratación.
Para la separación de aceites, se ha modificado el puente del decantador, colocando unas rasquetas que los arrastran y envían a un separador coalescente.
Con estas modificaciones, que han supuesto una inversión de unos 350.000 euros, se reduce el volumen de residuo de “lodos con aceite y cascarilla”.
En el área de la eficiencia energética, desde el año 2011 se vienen implantando mejoras en el horno de laminación para reducir el consumo de gas natural e incrementar el rendimiento energético. Este proyecto comenzó con un estudio sobre el estado del horno y los potenciales ahorros que se podían obtener con las tecnologías Honeywell. En una segunda fase se invirtieron 115.000 euros en equipos de medición y sistemas de control “on-line” para la monitorización y ajuste del proceso de combustión.
El impacto de estas acciones, junto a las modificaciones en los métodos de trabajo, ha permitido reducir un 11% las emisiones de CO2 en el año 2013 respecto a 2010.