Dos proyectos desarrollados en Granada buscan recuperar de forma eficaz plásticos como el polietileno, el polipropileno y el poliestireno presentes en los residuos sólidos urbanos.
El plástico se ha convertido en un elemento cotidiano en nuestras vidas. A pesar de intentar cumplir durante los últimos años la regla de las 4 R (Reducir, Reutilizar, Reciclar y Recuperar), en 2018 se recogieron 29,1 millones de toneladas de plástico de los residuos posconsumo, de los cuales aproximadamente solo el 32,5% fueron reciclados, según datos publicados por la asociación industrial PlasticsEurope. El resto fue destinado a valorización energética y a depósito en vertedero, lo que está muy lejos de alcanzar los objetivos de recuperación marcados por la UE. En este contexto, surgen los proyectos LIFE4FILM y LIFEPLASMIX.
Ambas iniciativas, financiados por el Programa LIFE de la Unión Europea, tienen como objetivo recuperar el plástico film y plástico mezcla contenidos en los residuos municipales y evitar su eliminación mediante vertederos o incineradoras, volviendo así a darle una segunda vida.
Parte del proyecto se desarrolla en la planta de tratamiento de residuos La Ecocentral Granada, sita en la localidad de Alhendín, así como en el cercano polígono industrial de Marchalhendín, de cara a minimizar y optimizar el impacto ambiental asociado con el transporte y logística.
PROYECTO LIFE 4 FILM
El proyecto ‘LIFE4FILM: Post-consumption film plastic recycling from municipal solid waste’, tiene como objetivo principal implementar una demostración piloto de una solución integrada a través de tecnologías de reciclaje innovadoras para la separación del film de polietileno (PE) contenido en el flujo de los residuos sólidos urbanos (RSU) y su reutilización en forma de bolsas plásticas como productos finales.
En el proyecto, liderado por FCC Medio Ambiente, participan socios como Aimplas, Grupo Stadler, Grupo Lindner, Erema, Universidad de Granada e Ibañez Extrusoras.
La planta preindustrial está diseñada para tratar 1,40 toneladas/h (10.000 t/año) de residuos de plástico film de PE procedente de RSU, produciendo aproximadamente 500 kg/h de material reciclado (4.000 t/año). Consta de cuatro etapas principales: separación, lavado, extrusión y soplado, tal y como se puede observar en la siguiente imagen. Además, la planta contará con un proceso de tratamiento de efluentes generados en la etapa de lavado.
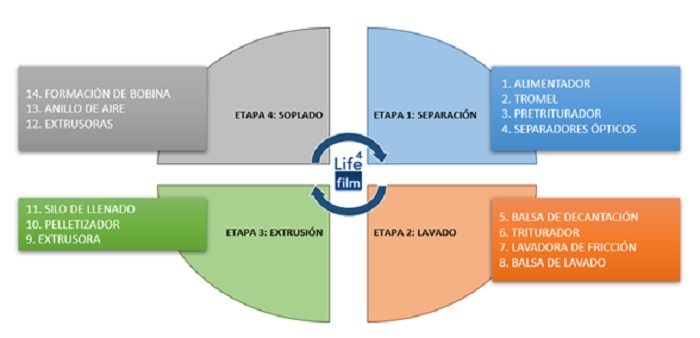
Etapa 1: Separación
El plástico film recuperado en la planta de tratamiento de residuos es utilizado como materia prima en esta etapa e introducido en un trómel para la apertura y separación de materiales impropios. El rebose de este trómel, se precipita a un triturador que reduce el tamaño del material. El material triturado es transportado a un separador balístico, el cual elimina del flujo los materiales “rodantes”. Además, durante este trayecto, un separador magnético retira los restos férricos que se pueda encontrar en el flujo.
A continuación, el material plástico atraviesa una cascada de tres separadores ópticos para alcanzar una pureza válida para las siguientes etapas y que el producto se pueda valorizar.
Etapa 2: Lavado
Con el objetivo de una mejor manipulación del material seleccionado en la etapa anterior, es triturado a un tamaño menor. Una vez triturado, el material se conduce a un prelavado para la eliminación de elementos que puedan dañar los equipos posteriores. A continuación, el material es introducido en la línea de lavado, eliminando la suciedad adherida.
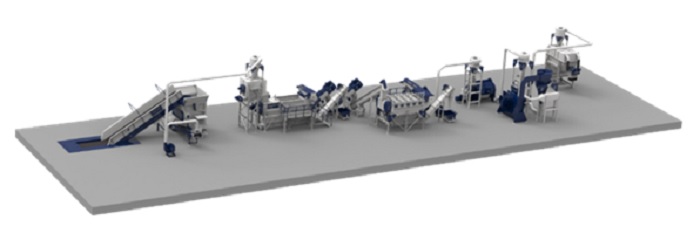
Esta etapa dispone de un sistema de tratamiento que permitirá la reutilización de la mayor parte de agua y el vertido de la restante bajo las exigencias ambientales requeridas.
Tras la limpieza del material, este es secado mediante dos secadores mecánicos en serie, que eliminan la gran parte de agua del flujo, y una unidad de secado térmico mediante aire caliente para reducir los niveles de humedad para la siguiente etapa.
Etapa 3: Extrusión
En la etapa de extrusión, el material lavado y seco es transformado en pellets mediante presión y calor, empleando un sistema innovador de filtración ultrafina y desgasificación.
Etapa 4: Soplado
Tras la extrusora, la granza obtenida es transformada en una lámina de plástico con el objetivo de generar un material apto para fabricar bolsas recicladas.
PROYECTO LIFEPLASMIX
El proyecto ‘LIFEPLASMIX: Plastic mix recovery and PP&PS recycling from municipal solid waste’, tiene como misión recuperar y reciclar los residuos de plástico mezcla contenidos en los residuos sólidos urbanos, valorizando el polipropileno (PP) y poliestireno PS (GPPS, HIPS, EPS, XPS) en granza o escamas recicladas de calidad apta para ser empleada para la fabricación de nuevos productos.
En este proyecto, liderado también por FCC Medio Ambiente, participan como socios Grupo Stadler, Grupo Lindner, Universidad de Granada, Pellenc ST, Andaltec y Anaip.
El proyecto desarrollará tecnologías innovadoras en una planta de reciclaje preindustrial que producirá aproximadamente 3.769 toneladas/año de material reciclado, una nueva solución de reciclaje rentable basada en la separación óptica, lavado y extrusión que llevará a la reducción del 90% de residuos de PP y PS. Consta de tres etapas principales: separación, lavado y secado, y extrusión, tal y como se puede observar a continuación. Además, la planta cuenta con un proceso de tratamiento de efluentes generados en la etapa de lavado.
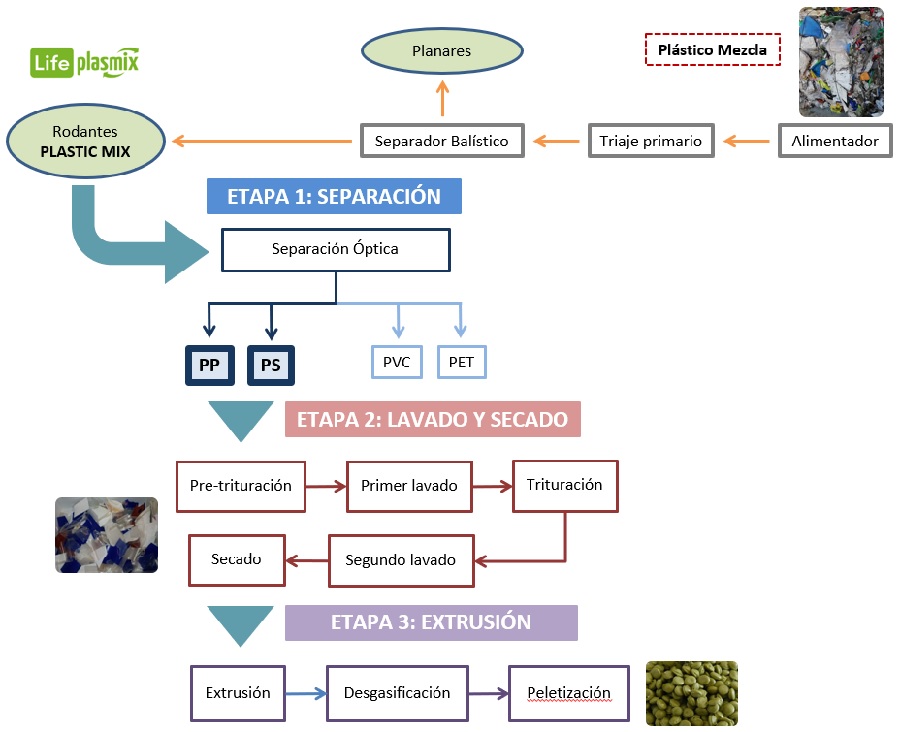
Etapa 1: Clasificación
La etapa de separación se ubica en la Ecocentral, junto con las instalaciones del proyecto LIFE4FILM. Las balas de plástico mezcla de RSU recuperadas en la planta de tratamiento son introducidas en un triturador-alimentador. Posteriormente, el material es transportado hasta un separador balístico, donde el material se separa en planares y rodantes.
Los rodantes, el material plástico de interés en este proceso, atraviesan una cascada de tres separadores ópticos configurados para la separación de PP y los distintos tipos de PS.
Etapa 2: Lavado y secado
Tras el proceso de clasificación, el material plástico se introduce en el alimentador de la línea de lavado. Esta etapa se llevará a cabo de forma similar a la descrita para el proyecto LIFE4FILM.
Etapa 3: Extrusión
Hasta el momento, la etapa de extrusión se realizará fuera de las instalaciones de la planta piloto, ya que no se cuenta con un socio tecnológico que aporte el equipo. Se estudiará una vez que empiece a producir material y la calidad de este para su transformación de escamas a pellets.
Actualmente ambos proyectos han finalizado con el montaje mecánico de la etapa de lavado, dando comienzo a la instalación eléctrica de la misma. Por otro lado, el montaje mecánico de la etapa de extrusión del proyecto LIFE4FILM también ha sido completado.
Con estos dos proyectos se conseguirá, además de las mejoras en concepto de recuperación y reciclaje del material indicado, reducir las emisiones de CO2 en la industria del plástico, minimizando, por tanto, la huella de carbono, y siendo ambos proyectos además un gran avance para el apoyo de la economía circular del plástico.