El proceso recién descubierto es una prueba de concepto de una estrategia de reciclado que puede aplicarse a la inmensa mayoría de las palas de aerogeneradores, así como a otros materiales de base epoxi.
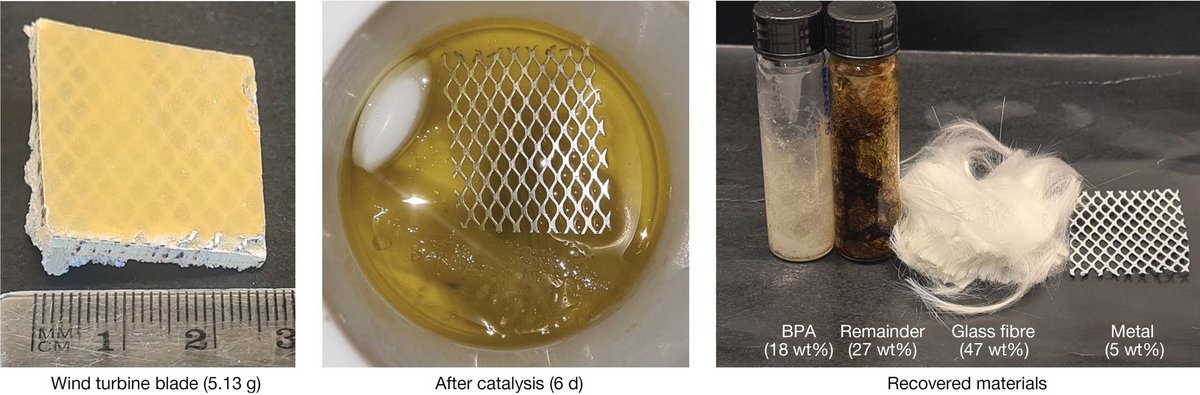
Investigadores de la Universidad de Aarhus y el Instituto Tecnológico Danés han desarrollado un proceso de reciclaje químico capaz de desmontar el compuesto epoxídico de las palas de aerogeneradores y extraer simultáneamente fibras de vidrio intactas, así como uno de los componentes básicos originales de la resina epoxi. Los materiales recuperados podrían utilizarse en la producción de nuevas palas.
El nuevo proceso químico no se limita a las palas de los aerogeneradores, sino que funciona en muchos de los denominados compuestos epoxídicos reforzados con fibras, incluidos algunos materiales reforzados con fibras de carbono, especialmente costosas.
Así, el proceso puede contribuir a establecer una economía circular potencial en las industrias de turbinas eólicas, aeroespacial, automovilística y espacial, donde estos compuestos reforzados, debido a su ligereza y larga durabilidad, se utilizan para estructuras portantes.
Precisamente, la durabilidad de las palas plantea un reto medioambiental. La mayoría de las palas de aerogeneradores acaban en vertederos cuando se desmantelan, porque son extremadamente difíciles de descomponer. Si no se encuentra una solución, en 2050 habremos acumulado 43 millones de toneladas de residuos de palas de aerogeneradores en todo el mundo.
El proceso recién descubierto es una prueba de concepto de una estrategia de reciclado que puede aplicarse a la inmensa mayoría de las palas de aerogeneradores existentes y en producción, así como a otros materiales a base de epoxi.
Los resultados acaban de publicarse en la prestigiosa revista científica Nature. En concreto, los investigadores han demostrado que utilizando un catalizador a base de rutenio y los disolventes isopropanol y tolueno, pueden separar la matriz epoxi y liberar uno de los componentes básicos originales del polímero epoxi, el bisfenol A (BPA), y fibras de vidrio totalmente intactas en un solo proceso.
Sin embargo, el método aún no es escalable de forma inmediata, ya que el sistema catalítico no es lo bastante eficiente para su aplicación industrial, y el rutenio es un metal raro y caro. Por ello, los científicos de la Universidad de Aarhus siguen trabajando para mejorar esta metodología.
«No obstante, lo consideramos un avance significativo para el desarrollo de tecnologías duraderas que puedan crear una economía circular para los materiales a base de epoxi», afirma Troels Skrydstrup, profesor del Departamento de Química y del Centro Interdisciplinario de Nanociencia (iNANO) de la Universidad de Aarhus, quien asegura también que»se trata de la primera publicación de un proceso químico que puede desmontar selectivamente un compuesto epoxi y aislar uno de los bloques de construcción más importantes del polímero epoxi, así como las fibras de vidrio o carbono, sin dañar estas últimas en el proceso».
La investigación cuenta con el apoyo del proyecto CETEC (Circular Economy for Thermosets Epoxy Composites), que es una asociación entre Vestas, Olin Corporation, el Instituto Tecnológico Danés y la Universidad de Aarhus.